Инструкция По Са-3
Инструкция по ремонту автосцепки са 3 Инструкция по ремонту и обслуживанию автосцепного. 3 Подготовка к ремонту.2.4 Разборка механизма автосцепки СА — 3. Для заметок Мвпс цт-0058, Инструкции по ремонту тормозного оборудования вагонов цв-цл-0013, а также указаний. 2.2.7 и 2.2.20 настоящей Инструкции ) и направляют в КПА или отделение по ремонту автосцепки.При этом на каждый утилизированный корпус автосцепки составляется акт. Краткая характеристика автосцепки СА — 3 1.1 Назначение 1.2 Значение автосцепки СА — 3 1.
Понедельник, 18 апреля 2016 г. Разборка и сборка механизмов автосцепки СА-3. 2:10 автосцепное оборудование, Вагонник. Сборка автосцепки. Сборка автосцепки: Установить замкодержатель и подъемник в автосцепку. Установить предохранитель на шип замка. Установить замок с предохранителем в автосцепку, поднимая хвостик предохранителя ломиком, одновременно нажимая на замок.. Инструкция по сигнализации на железнодорожном транспорте РФ. Приложение №7 к приказу Минтранса России от г. №162 Главы I, II. Инструкция по ремонту и обслуживанию. Расположение автосцепного устройства СА-3.
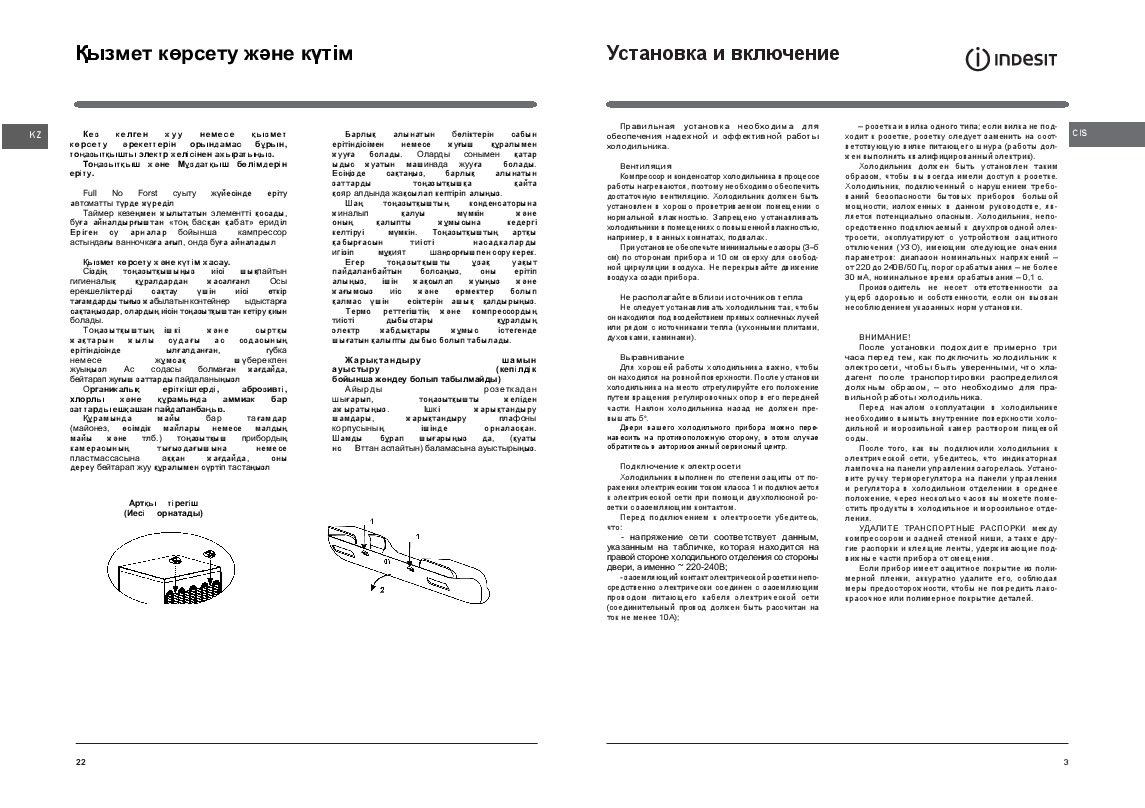
9 Замок автосцепки.Проверяется замок шаблонами в соответствии с Инструкцией ЦВ-ВНИИЖТ-494-97.Краткая характеристика автосцепки СА — 3. Ремонт автосцепки СА — 3.2.1 Система технологического обслуживания и ремонта вагонов.Размещение технологической оснастки в пунктах ремонта автосцепного устройства должно обеспечивать выполнение требований настоящей Инструкции, а.2.5 Ремонт автосцепки СА — 3.
Автосцепка СА — 3 состоит из.Назначенный срок службы автосцепки при соблюдении правил эксплуатации и хранении не менее 2 лет до первого деповского ремонта.Инструкция по ремонту и обслуживанию автосцепного устройства подвижного состава железных дорог СССР (утв. Автосцепное устройство.

Тяговый хомут автосцепки СА 3 Инструкция по ремонту. Мпс СССР n цв/4006). Тяговый хомут автосцепки СА — 3. При этом на каждый утилизированный корпус автосцепки составляется акт. Ремонт автосцепки СА — 3.
2.24), была прижата к торцовой поверхности замка, а основание 2 шаблона прилегало к боковой поверхности замка. Замок признают годным, если при перемещении шаблона вниз проходная часть гребенки 3 проходит мимо шипа для предохранителя, а непроходная не проходит. Диаметр шипа замка для предохранителя проверяют непроходным и проходным стаканами этого шаблона (рис. Шип 1 считают годным, если проходной стакан 2 свободно надевают на него до упора торцом в замок у основания шипа, а непроходной стакан 3 не надевается или надевается частично так, что торец шипа не выступает за верхнюю кромку кольца непроходного стакана.
Износ прилива для шипа по поверхности, очерченной радиусом 24 мм проверяется шаблоном 833р как показано на рис. Зазор а более 3 мм не допускается.
Направляющий зуб замка должен соответствовать очертаниям шаблона 943р (рис. Шаблон своим вырезом должен проходить по всей ширине зуба, причем суммарный зазор между кромками зуба и шаблоном не должен превышать 2 мм. Замок со вставкой автосцепки СА-ЗМ считают неисправным, если: а) диаметр отверстия в замке для валика более 17 мм, а отверстия вставки более 17,5 мм. Такие отверстия надо заварить и просверлить вновь с соблюдением размеров, указанных на рис.
2.28; б) замыкающая поверхность вставки не отвечает требованиям проверки шаблонами 852р и 899р. В этом случае замыкающая часть должна быть восстановлена наплавкой с последующей обработкой и проверкой указанными шаблонами; в) диаметр валика замка менее 15,5 мм или на нем имеются трещина или изгиб, препятствующий свободному перемещению вставки в замке. Валик с любым из этих дефектов надо заменить новым. В остальном замок со вставкой должен отвечать тем же требованиям, что и замок автосцепки СА-3. После ремонта замок проверяют шаблонами 852р, 839р, 833р и 943р, как указано выше.
Замкодержатель 2.1.28. Замкодержатель признают неисправным и направляют в ремонт, если: а) он погнут или его толщина и ширина лапы не соответствуют очертаниям вырезов шаблона 841р; б) овальное отверстие, расцепной угол, упорная часть противовеса не соответствуют требованиям проверки шаблоном 826р; в) наружное очертание (контур) замкодержателя не соответствует шаблону 916р; г) имеется трещина. Толщину замкодержателя и возможные изгибы проверяют шаблоном 841р (рис. 2.29), который надевают на замкодержатель вначале вырезом, охватывающим противовес и стенку замкодержателя. Шаблон должен дойти до верхней плоскости лапы (положение 7), затем его поворачивают наклонно (положение II) так, чтобы лапа замкодержателя вошла в соответствующий вырез шаблона.
Замкодержатель годен, если он свободно проходит через вырез шаблона. Далее проверяют ширину лапы замкодержателя непроходным вырезом этого шаблона, который надвигают на лапу. Рабочая поверхность лапы должна быть параллельна кромке шаблона (положение III). Лапа не должна входить в непроходной вырез. Расстояние а (рис. 2.30, а) от передней боковой поверхности стенки овального отверстия до упорной поверхности противовеса замкодержателя проверяют шаблоном 826р.
Для этого замкодержатель навешивают овальным отверстием на опору 1 так, чтобы противовес его был обращен вниз, и поворотом замкодержателя против часовой стрелки подводят противовес к сухарю 2. Замкодержатель считают годным, если упорная поверхность противовеса проходит мимо проходной части сухаря 2 и не проходит мимо непроходной (поз.
7), и негодным, если противовес проходит мимо непроходной части сухаря или не проходит мимо проходной (поз. Высоту угла противовеса замкодержателя 9 проверяют этим же шаблоном (рис. Замкодержатель навешивают овальным отверстием на опору 1 так, чтобы лапа замкодержателя прилегала к угольнику 7, а боковая поверхность была прижата к поверхности фланца опоры 7 и опорной планке 8 шаблона.
Высота угла противовеса считается правильной, если проходная часть планки 5, поворачиваемой по часовой стрелке, проходит мимо угла противовеса замкодержателя, а непроходная не проходит (замкодержатель годен, поз. Если проходная часть сухаря не проходит или непроходная часть проходит мимо противовеса, то высота считается неправильной, замкодержатель негоден (поз. При этой же установке производят проверку расцепного угла замкодержателя. Проходная часть планки б, поворачиваемой против часовой стрелки, должна пройти мимо угла, а непроходная не должна (Замкодержатель годен, поз.
Если проходная часть планки б не проходит мимо расцепного угла или непроходная проходит, замкодержатель негоден (поз. Для проверки размеров овального отверстия замкодержателя используют пробки 3 и 4 шаблона 826р (рис. Ширину овального отверстия считают правильной (поз. 7), если Замкодержатель не надевается на непроходную пробку 4 или надевается частично, но не доходит до упора в лист шаблона. Ширина овального отверстия бракуется, если замкодержатель надевается на непроходную пробку 4 (поз.
Длину овального отверстия считают правильной (поз. III), если замкодержатель не надевается на непроходную часть пробки 3. Длину овального отверстия бракуют, если: замкодержатель не надевается на верхнюю удлиненную часть пробки шаблона (поз. IV); стержень пробки не проходит по всей длине отверстия (поз. V); замкодержатель не надевается (поз. VI) на проходную часть или надевается (поз.
VII) на непроходную часть пробки шаблона. Наружное очертание замкодержателя проверяют шаблоном 916р, как показано на рис. Замкодержатель годен, если его боковая стенка плотно лежит на плите шаблона, а профильная призма а шаблона своим выступом касается упора б или зазор между ними не превышает 1 мм. После ремонта замкодержатель должен быть проверен шаблонами 841р, 826р, 916р, как указано выше. Предохранитель 2.1.33. Предохранитель признают неисправным и направляют в ремонт, если: а) он погнут; б) диаметр отверстия, длина верхнего плеча, высота его торца или очертания верхнего и нижнего плеч не соответствуют шаблону 800р-1; в) имеется трещина. Наличие изгиба предохранителя определяют, пропуская его в вырезы а и б шаблона 800р-1 (рис.
Если предохранитель не проходит в вырезы, то его надо выправить. Пропуская предохранитель через вырез а, надевают его отверстием на шип 7, укрепленный в обойме 2, до упора в основание. Предохранитель годен, если он свободно проходит через вырез в листе шаблона и располагается заподлицо с верхней плоскостью листа или ниже ее. При проверке толщины плеч в вырезе б через отверстие предохранителя пропускают стержень 3 и затем поворачивают предохранитель на нем по часовой стрелке и обратно настолько, чтобы верхнее и нижнее плечи полностью прошли через соответствующие ветви выреза в шаблоне. Диаметр отверстия в предохранителе проверяют непроходной пробкой 4 шаблона. Предохранитель считается годным, если он не надевается на пробку с обеих сторон, или надевается на нее, но не доходит до упора в лист шаблона.
Для проверки длины верхнего плеча предохранитель надевают на опорный шип 5 шаблона и поворачивают на нем против часовой стрелки. Предохранитель годен, если нижний угол торца верхнего плеча проходит мимо проходной части сухаря б и не проходит мимо непроходной. Высоту торцовой поверхности верхнего плеча предохранителя проверяют непроходным вырезом 7 шаблона. Предохранитель исправен, если торцовая часть его верхнего плеча не полностью входит в вырез, т. Остается зазор.
После ремонта предохранитель проверяют шаблоном 800р-1, как указано выше. Подъемник замка 2.1.35. Подъемник замка признают неисправным и направляют в ремонт, если любой из его проверяемых размеров не соответствует требованиям проверки шаблоном 847р (рис. 2.33), и исправным, если: а) подъемник, надетый на пробку 2, входит в обойму 5; б) проходит в вырез 7; в) буртиком входит в вырез б; г) отверстием не надевается на пробку 7; д) надетый на пробку 3, не подходит широким пальцем под шляпку стойки 4, а узким пальцем проходит мимо проходной части сухаря 8 и не проходит мимо непроходной. После ремонта подъемник замка проверяют шаблоном 847р, как указано выше.
Валик подъемника 2.1.36. Валик подъемника признают неисправным и направляют в ремонт, если любой из его проверяемых размеров не соответствует требованиям проверки шаблоном 919р (рис. 2.34), и исправным, если: а) цилиндрические части стержня проходят в соосно расположенные большое 2 и малое 7 кольца шаблона и вращаются в них; б) стержень валика не проходит цилиндрической частью большего диаметра в вырез 8, а меньшего диаметра - в вырез 7; в) цилиндрическая часть большего диаметра не проходит по длине в вырез б и проходит в вырез 4; г) паз для крепящего болта, установленный на контрольный буртик 3, полностью закрывает его; д) квадратная часть стержня проходит в отверстие 5 и не проходит в вырез 7. После ремонта валик подъемника проверяют шаблоном 919р, как указано выше. Проверка собранной автосцепки 2.1.37.
Контур зацепления собранной автосцепки проверяют проходным шаблоном 828р, при этом лапу замкодержателя вжимают заподлицо с ударной поверхностью зева корпуса (рис. Шаблон должен свободно проходить по всей высоте головы автосцепки.
При этом плоскость шаблона должна быть перпендикулярна к ударной стенке зева. Зазоры между шаблоном и проверяемыми поверхностями не контролируются. Проверку действия механизма автосцепки выполняют в следующем порядке: проверяют действие предохранителя замка от саморасцепа; убеждаются в отсутствии преждевременного включения предохранителя; контролируют обеспечение удержания механизма в расцепленном положении; выявляют возможность расцепления сжатых автосцепок (т. Когда лапа замкодержателя прижата заподлицо с ударной стенкой зева); проверяют уход замка от вертикальной кромки малого зуба при включенном предохранителе; контролируют расстояние от вертикальной кромки малого зуба до кромки замка в его нижнем свободном положении и от кромки замка до кромки лапы замкодержателя по горизонтали; проверяют положение лапы замкодержателя относительно ударной стенки зева, когда замок находится в заднем крайнем положении.
Для проверки действия предохранителя от саморасцепа шаблон 820р устанавливают в зеве собранной автосцепки так, чтобы он ребром со стороны непроходного выреза 27 мм нажимал на лапу замкодержателя и своим листом прилегал к носку большого зуба (рис. При этом упоры а должны быть прижаты к ударной стенке зева. Для определения правильного положения шаблона служит выступ. При капитальном ремонте вагонов и локомотивов используется аналогичный шаблон, но с вырезом 29 мм. Предохранитель считают действующим, если при указанном положении шаблона замок от нажатия на его торец уходит внутрь кармана корпуса только до упора предохранителя в противовес замкодержателя (поз. Если же замок уходит внутрь кармана полностью (поз. II), значит механизм автосцепки неисправен.
Мри Фнс 3 По Рт
Для выявления возможности опережения, т. Преждевременного включения предохранителя при сцеплении, шаблон 820р устанавливают так, чтобы он ребром со стороны проходного выреза 35 мм нажимал на лапу замкодержателя и своим листом прилегал к носку большого зуба (рис.
При этом упоры б должны быть прижаты к ударной стенке зева. Механизм автосцепки считают годным, если при нажатии на торец замок беспрепятственно уходит в карман корпуса на весь свой ход (поз. Если же замок при нажатии на него не уходит полностью внутрь корпуса (поз. II), то автосцепка негодна. Для проверки надежности удержания замка в расцепленном положении до разведения вагонов шаблон 820р устанавливают так, чтобы на лапу замкодержателя нажимало ребро со стороны выреза 25 мм (рис.
2.38) с надписью 'Проверка расцепления'. Удерживая шаблон в таком положении, поворотом валика подъемника уводят замок до отказа внутрь кармана корпуса, а затем освобождают валик. Автосцепка считается годной (поз.1), если замок удерживается в верхнем положении до тех пор, пока лапа замкодержателя прижата ребром шаблона, и если он опускается под действием своего веса после прекращения нажатия, причем другие детали механизма беспрепятственно возвращаются в исходное положение.
Автосцепка негодна (поз. II), если замок, уведенный валиком подъемника, не удерживается в расцепленном (поднятом) положении. Для определения возможности расцепления автосцепок, когда лапа замкодержателя прижата заподлицо со стенкой зева (положение в сжатом составе), нужно прямолинейным ребром шаблона 820р нажать на лапу замкодержателя так, чтобы ребро по всей длине прилегало к ударной стенке зева автосцепки, причем лист шаблона должен быть прижат к носку большого зуба (рис. Удерживая шаблон в таком положении, поворачивают валик подъемника до отказа, чтобы увести замок на весь ход и поставить механизм в расцепленное положение. Автосцепка годна, если при движении замка лапа замкодержателя не отжимает шаблон от ударной стенки зева, механизм удерживается в положении расцепления и все детали его после отвода шаблона беспрепятственно возвращаются в исходное положение. Если лапа замкодержателя отталкивает шаблон, значит проход для верхнего плеча предохранителя между потолком корпуса автосцепки и противовесом замкодержателя недостаточен, т. Механизм автосцепки неисправен.
Величину отхода замка от вертикальной кромки малого зуба проверяют шаблонами 820р и 787р (рис. Для проверки нажимают на лапу замкодержателя непроходной стороной шаблона 820р со стороны выреза 27 мм.
Сохраняя такое положение, нажимают шаблоном 787р на торец замка вверху и у начала скоса вертикальной кромки сначала проходной стороной с цифрой 7 (положение I), а затем непроходной с цифрой 16 (положение III). Автосцепка считается исправной, если в положении 1 замок уходит в карман корпуса до упора шаблона в ударную поверхность малого зуба, а в положении III между шаблоном и поверхностью малого зуба остается зазор. Если шаблон 787р располагается относительно ударной поверхности малого зуба так, как показано в положениях II и IV, то механизм автосцепки негоден. Расстояние от вертикальной кромки малого зуба автосцепки до вертикальной кромки замка в его крайнем нижнем положении должно быть 2-8 мм; от кромки замка до кромки лапы замкодержателя по горизонтали - не менее 20 мм, а для замкодержателей; не имеющих скоса на лапе, - не менее 9 мм (рис.
Замеры производят линейкой при свободном положении замка. Для проверки положения лапы замкодержателя относительно ударной стенки зева нажимают на замок, устанавливая его в заднее крайнее положение.
После этого нажимают на лапу, утапливая ее внутрь кармана корпуса (она не должна выходить в зев от ударной стенки). После проверки автосцепки в собранном состоянии при соответствии ее требованиям, изложенным в пп. 2.1.37 и 2.1.38, валик подъемника закрепляют болтом 1 (рис.
2.42) М 10х90 с гайкой 3, под головку болта и гайку ставят фасонные шайбы 2, которые загибают на головку болта и гайку. Автосцепка вагонов рефрижераторных секций, кроме концевой, должна иметь стопорный болт М 16х60, препятствующий ее расцеплению. ПОГЛОЩАЮЩИЕ АППАРАТЫ Поглощающие аппараты Ш-1-Т, Ш-1-ТМ, Ш-2-Т, Ш-2-В 2.2.1. При капитальном ремонте грузовых вагонов и локомотивов поглощающие аппараты должны быть разобраны и негодные детали заменены. При разборке аппарата необходимо на клиньях и на корпусе сделать соответствующие пометки, чтобы при сборке (в случае исправных деталей) клинья были поставлены на прежние места.
При других видах периодического ремонта разбирают только неисправный поглощающий аппарат и негодные детали заменяют. Снятый при ремонте подвижного состава (кроме капитального ремонта) поглощающий аппарат не подлежит разборке если: а) выход конуса (расстояние между торцом конуса и кромкой горловины корпуса аппарата) для аппаратов Ш-1-Т и Ш-1-ТМ не менее 70 мм, для Ш-2-Т - не менее 110 мм, для Ш-2-В - не менее 90 мм; б) отсутствуют трещины, изломы в деталях аппарата; в) толщина стенки корпуса в зоне контакта с клином не менее 14 мм; г) отсутствует даже легкое качание деталей аппарата, что определяется ударами молотком по ним; д) габариты аппарата соответствуют требованиям проверки шаблоном 83р (83р-1) (рис.
При несоответствии указанным требованиям аппарат должен быть разобран и отремонтирован. Допускаются к сборке: а) корпус аппарата с толщиной стенки не менее 18 мм при капитальном ремонте вагонов и локомотивов и не менее 16 мм при всех других видах периодического ремонта подвижного состава; отремонтированный сваркой корпус поглощающего аппарата при условии, что после разделки трещин в зоне технологических отверстий и усиливающих ребер суммарная длина их не превышает 120 мм; б) фрикционные клинья с толщиной стенки не менее 17 мм для аппаратов Ш-1-Т и Ш-1-ТМ (рис. Проходной шаблон 83р для проверки габаритных размеров собранного поглощающего аппарата 2.45, размер а) и не менее 32 мм для аппаратов Ш-2-В и Ш-2-Т (размер б); в) нажимной конус с износом не более 3 мм при проверке шаблоном 611 (рис. 2.46) для аппарата Ш-1-ТМ и 611-1 для аппарата Ш-2-В; г) нажимная шайба с износом не более 5 мм; д) стяжной болт с износом не более 5 мм и длиной нарезки не более 35 мм; е) пружины с высотой в свободном состоянии, не менее: наружная 390 мм, внутренняя 362 мм для аппаратов Ш-1-Т и Ш-1-ТМ; наружная 353 мм, внутренняя 375 мм для аппарата Ш-2-Т и наружная 395 мм, внутренняя 360 мм для аппарата Ш-2-В; пружина с изломом оттянутого конца на длине менее 1/3 длины окружности (сломанный конец должен быть поставлен на дно корпуса). Пружина с изломом оттянутого конца на длине более 1/3 длины окружности к сборке не допускается. После сборки до постановки гайки стяжного болта у аппаратов Ш-1-Т и Ш-1-ТМ выход конуса а должен быть не менее 80 мм, у аппаратов Ш-2-Т - не менее 120 мм, у аппаратов Ш-2-В - не менее 105 мм, причем зазор между нажимным конусом и шайбой менее 4 мм (рис.
2.47, а) для аппаратов Ш-1-Т и Ш-1-ТМ не допускается. Для определения величины этого зазора сначала ставят нажимной конус непосредственно на нажимную шайбу и измеряют расстояние от кромки корпуса до торцовой поверхности конуса. Затем конус ставят, как обычно, на фрикционные клинья, и измеряют то же расстояние; разность между результатами измерений и будет величиной зазора. Измерения проводят в трех местах, равномерно расположенных по периметру.
Габаритные размеры отремонтированных и собранных аппаратов Ш-1-Т, Ш-1-ТМ и Ш-2-В должны быть проверены шаблоном 83р, аппарата Ш-2-Т - тем же шаблоном, но с увеличенным по ширине проемом (83р-1). После проверки аппарата и постановки гайки конец стяжного болта над гайкой должен быть расклепан для предупреждения ее самоотвинчивания. Чтобы не было затруднений при постановке собранного аппарата на локомотив или вагон, его необходимо дополнительно сжать на прессе и под гайку стяжного болта поставить металлическую прокладку высотой 15-20 мм, изготовленную из стального прутка диаметром 16-20 мм (рис. Такие форма и размеры прокладки обеспечат свободное ее выпадение при первом сжатии аппарата после установки на вагон или локомотив. Рекомендуется использовать для сжатия поглощающего аппарата в хомуте также и переносной гидравлический пресс. Аппарат Ш-2-В устанавливают на подвижной состав, имеющий ударную розетку, обеспечивающую расстояние от упора головы автосцепки до розетки не менее 100 мм (при касании торцом хвостовика автосцепки упорной плиты). Окрашивать фрикционные клинья, поверхности трения нажимного конуса и внутреннюю поверхность корпуса аппарата запрещается.
Чтобы избежать разрыва корпуса, запрещается устанавливать: а) фрикционные клинья в углы корпуса, где образовались выступы неизношенного металла; б) прокладки под пружины поглощающего аппарата. Поглощающий аппарат Ш-6-ТО-4 2.2.7. При поступлении вагона в деповской ремонт производится осмотр аппарата на вагоне. Для осмотра аппарата необходимо снять поддерживающую планку, предварительно закрепив аппарат от возможного выпадения с помощью хомутов или подпорок. Аппарат считается исправным и не требует снятия с вагона, если: а) он плотно прилегает к задним упорам и через упорную плиту к передним упорам; б) толщина перемычки хомутовой части в отверстии для клина не менее 50 мм; в) толщина стенки горловины не менее 16 мм; г) фрикционные клинья плотно прилегают к стенкам корпуса и между ними одинаковый зазор; д) вкладыши расположены в пределах корпуса аппарата; е) крышка располагается относительно стенок хребтовой балки симметрично; ж) в деталях аппарата отсутствуют трещины в видимой зоне; з) износ тяговой полосы хомутовой части по толщине не более 5 мм. В случае, если аппарат не отвечает хотя бы одному из указанных требований, он должен быть снят с вагона, разобран и отремонтирован. При капитальном ремонте и через один деповской снятие аппарата производится независимо от его состояния.
Дата последнего полного осмотра определяется по клейму (см. 2.7 настоящей Инструкции). При капитальном ремонте вагонов осмотр аппарата производится с его полной разборкой. Допускаются к сборке детали аппарата со следующими размерами и износами элементов: а) толщина стенки горловины корпуса не менее 18 мм; б) толщина перемычек в отверстии для клина верхней и нижней тяговых полос хомутовой части не менее 50 мм; в) высота пружин, не менее: наружной цельной 598 мм, наружной большой 336 мм, наружной меньшей 260 мм, внутренних пружин 306 мм; г) излом оттянутого конца пружины на длине не более 1/3 длины окружности; д) износ рабочих поверхностей тяговых полос не более 4 мм; е) зазор между конусом и шайбой не менее 5 мм (проверяется, как указано в пп.
2.2.4); ж) износ фрикционных клиньев и конуса не более 3 мм; з) износ нажимной шайбы не более 5 мм; и) износы других деталей и их элементов не более 5 мм. Для проверки указанных выше нормативов допускается применение шаблонов по проекту ПКБ ЦВ Т 1295. После сборки аппарата проверяют выход конуса (должен быть не менее 130 мм) и выполняют работы, указанные в пп. Соединение аппарата с хвостовиком автосцепки допускается только с помощью клина, не имеющего буртиков. При постановке аппарата на вагон должна применяться поддерживающая планка с глубиной прогнутой части 10 мм. Поглощающие аппараты ПМК-110А и ПМК-ИОК-23 2.2.11. Поглощающие аппараты ПМК-110А и ПМК-110К-23 одинаковы по конструкции и отличаются только маркой металлокерамических элементов.
Инструкция По Са-3
Требования к их проверке, ремонту и обслуживанию едины и соответствуют изложенным в пп. Снятый при ремонте подвижного состава (кроме капитального ремонта) поглощающий аппарат (рис.
2.48) не подлежит разборке, если: а) выход конуса (расстояние в) не менее 110 мм; б) отсутствуют трещины, изломы его деталей и сквозные протертости корпуса; в) толщина стенки корпуса в рабочей части горловины не менее 16 мм; г) зазор б между торцом нажимного конуса и подвижной пластиной не менее 3 мм; д) отсутствует даже легкое покачивание деталей аппарата, что определяется постукиванием по ним молотком. При несоответствии хотя бы одному из указанных требований аппарат должен быть разобран и отремонтирован.